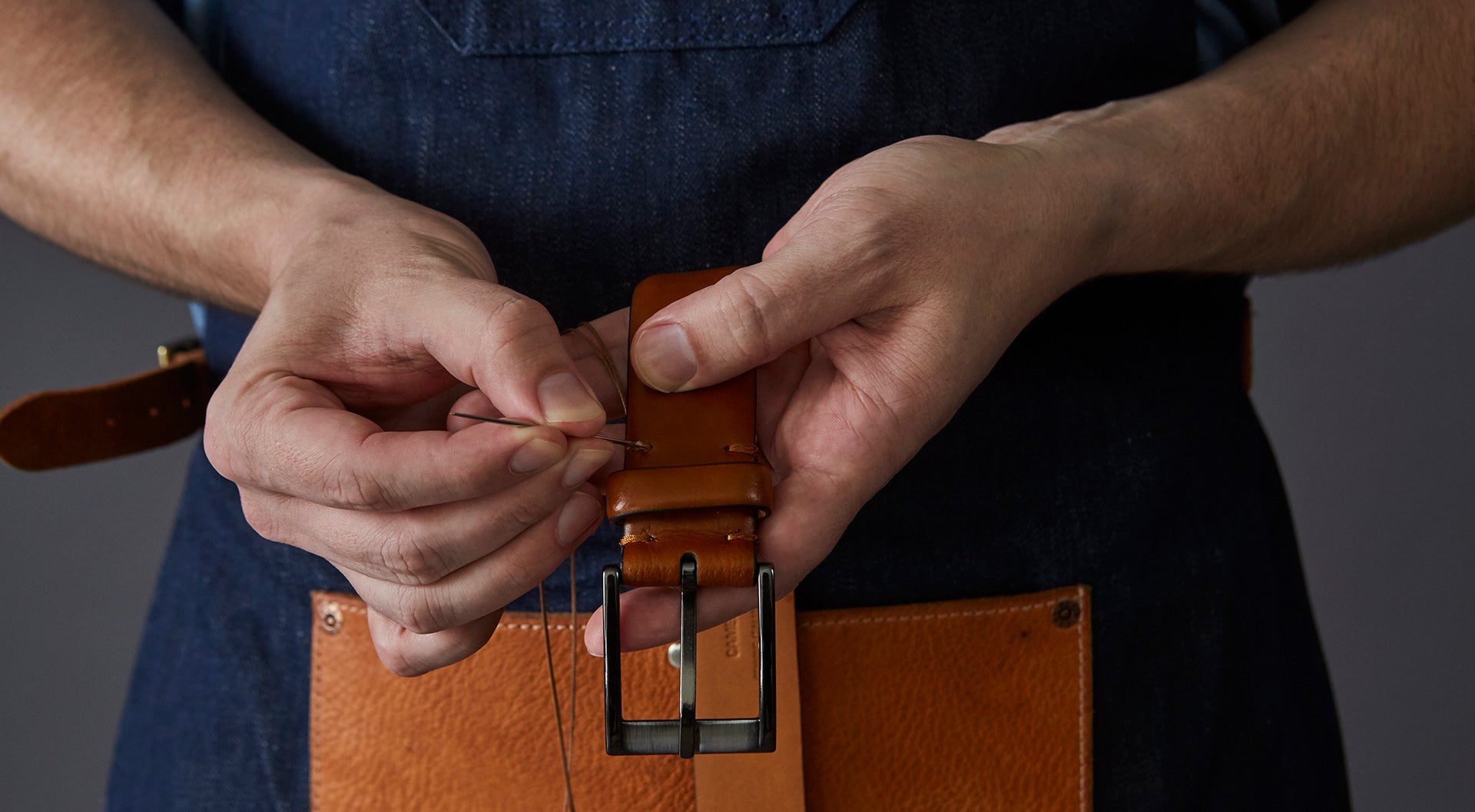
How Leather is Made
Leather is the heart and soul of Trafalgar, and as such, we consider ourselves leather experts. We take pride in our handcrafted, carefully designed pieces, and we want you to be able to appreciate your Trafalgar leather accessories as much as we do. Here is how our leathers are made from start to finish, so you can be a leather expert too.
The art of leather-making is a long, intricate process to turn a fresh cow hide into haberdashery-quality handmade wallets, shoes, belts, or handbags. All animal hides undergo the same beginning processes to become leather. It is the care and treatment that happens afterward which set our fine leathers apart from the rest.
The process starts with a hide, or animal skin, which the supplier removes from the animal and packs in salt. The salt will prevent spoiling during transit from the supplier to the tannery, where it will be processed into leather. The salt will draw out the excess moisture, as well as cure the hide to prevent decomposition. When properly frozen or air dried, a hide can last up to one year before undergoing the tanning process.

When the hides are ready to be processed, they are soaked in water for several days to remove the salt and any remaining hair, as well as rehydrate them. After soaking in water, the hides are placed in a lime solution, a process referred to as liming, to remove any remaining flesh and fur. They are then scraped to ensure a clean, even hide.
Liming the hides will also break down the collagen stiffened by the curing process, and make the hides more flexible. The hide may repeatedly be moved from acidic to basic solutions over several days, to gently further this collagen breakdown. The hides are then split into the top most layer, which will become high quality top and full grain leather, and the bottom most layers which can be processed into suede, nubuck, and coated leathers. When this process is complete, the hides are flexible and ready for tanning.
Tanning is the process of converting an animal’s hide into finished leather, which can later be turned into fine leather goods. This process varies slightly depending on the type and quality of leather being made, such as suede, Aniline, or embossed leathers. The aim of tanning is to retain the hide’s natural properties. The end result is a leather that is soft, flexible, and resistant to rotting when wet.
Animal hides consist of interwoven fibers made from collagen proteins. Tanning stabilizes the structure of collagen fibers, using chemical means to separate the fibers and lubricate them so the resulting leather becomes softer and more pliable. Finished leather is essentially preserved collagen fiber bundles.
The process of tanning involves soaking the hides in various chemical solutions as a means of breaking down the collagen and making the hide more chemically stable and durable. Tanning usually involves loading the hides into a drum or barrel and immersing them in tanning liquors as the drum gently rotates over time. This rotation agitates the hides to ensure they are fully coated in the tanning liquors, and also softens the hides over time.
Tanning liquors are the chemical solutions used to tan leather. These can include a variety of ingredients, but they all serve they same purpose. The two most popular types of tanning are Chrome Tanning and Vegetable Tanning.
Chrome tanning is a chemical-based method of tanning that was popularized during WWII. It is also the most popular method of tanning, for its fast processing time and soft, supple end result. This method involves using Chromium Sulfates to achieve collagen breakdown faster and more efficiently. Chrome Tanning results in a pale blue hide that needs to be dyed before use.
Vegetable Tanning utilizes the tannins found in tree bark and other plant and vegetable matter to produce leather. It is also the oldest method of tanning. Vegetable tanned leather often results in a light brown colored hide, which does not need to be dyed, unlike chrome tanned leathers. Vegetable Tanned Leathers have historically been used in shoemaking, book binding, and armor, as vegetable tanned leathers can easily be made very stiff. However, vegetable tanned leathers lack the resistance to discoloration and water damage that chemically tanned and stabilized leathers do.
After tanning to achieve the desired softness and pliability, the hides are then re-tanned to preserve the collagen and add dyes. When the hides are colored and tanned, they are then stretched, dried and rolled via machine to keep the leather pliable after extracted the water.
The final step is finishing. In this stage, leathers are given a top coat for sheen, water resistance, and lubrication. Leathers with imperfections may receive extra buffing, polishing, embossing, or trimming to perfect the surface and edges.
After finishing, the tanned leather is ready to be turned into your next favorite accessory.
